加州大學伯克利分校開發電荷編程沉積(CPD)3D打印技術,用于制造輕型高性能天線
導讀:隨著航空航天對輕量化的需求不斷增加,3D打印憑借結構優化優勢,成為雷達設計的理想選擇之一。
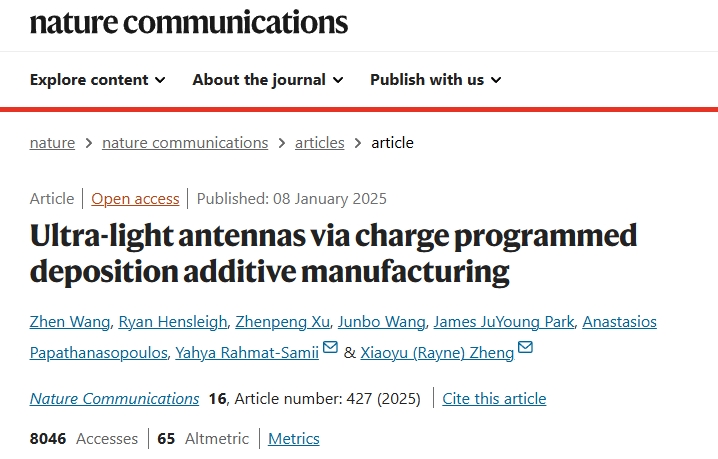
2025年4月24日,加州大學伯克利分校的研究人員開發了一種創新的3D打印技術——電荷編程沉積(CPD)。該技術能夠利用電荷引導的多材料沉積工藝,制造出超輕、結構復雜的天線。與傳統的光刻或減材制造工藝不同,電荷編程沉積能夠直接3D打印由金屬與電介質組成的復雜結構電磁設備.研究表明,使用市售桌面SLA打印機,CPD技術可以高效生產多種類型的天線,包括發射陣列、Vivaldi天線和喇叭天線。通過在單次打印中集成高導電性金屬和電介質材料,電荷編程沉積顯著減少了零件數量、重量和制造復雜度。此外,3D打印不受遠距離供應鏈的限制,通過數字文件直接生產,提升了效率和靈活性。它能夠減輕雷達系統重量,同時保持高性能,滿足航空航天對輕量化和高性能的嚴格要求。
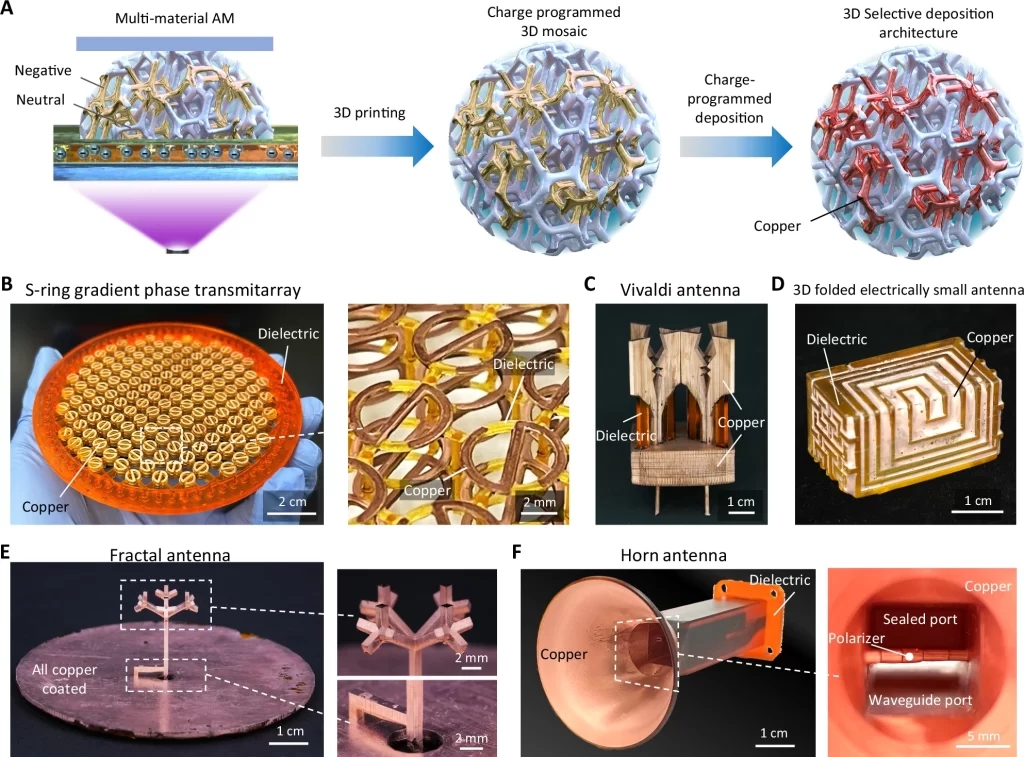
表面極性引導的3D打印
CPD工藝的核心基于電荷驅動的材料編程方法。在立體光刻打印過程中,研究人員將不同電荷極性(正電、負電或中性)分配到已打印的圖案化介電基板的各個區域。這種“電荷鑲嵌”方式決定了選擇性化學鍍過程中金屬的附著位置。只有與區域電荷相反的區域才能吸引金屬離子,從而精確地實現無刀具路徑的三維導電軌跡圖案化。
打印完成后,部件將經過一系列化學處理:鈀離子作為催化劑沉積在電荷區域,隨后銅被鍍到帶電區域。這項工藝能夠生成光滑且無裂紋的銅路徑,電導率為4.9×10⁷S/m,與退火銅相當,非常適合高頻應用。
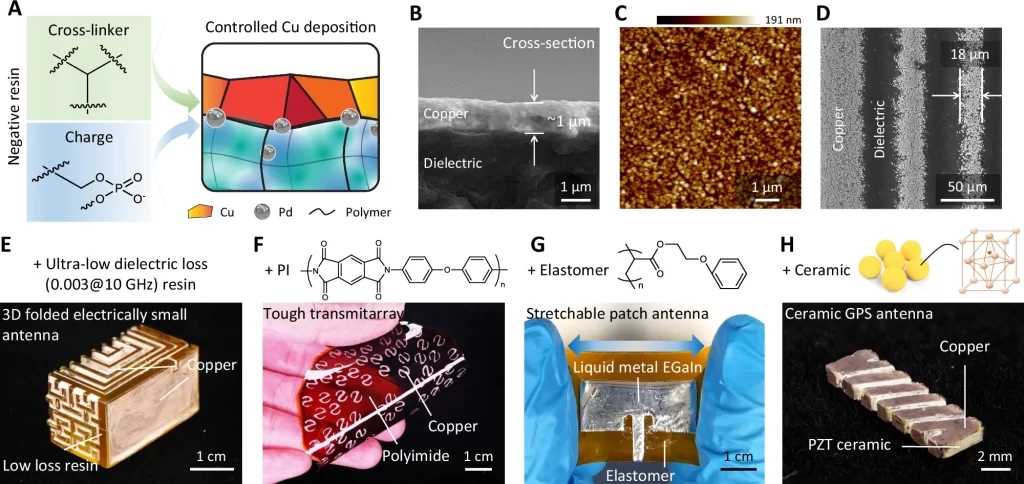
結構和功能的復雜性
研究人員通過制造一個圓極化19 GHz發射陣列天線,展示了這種方法的靈活性。該天線由三層互穿S環單元構成,重量僅為5克,相較于基于PCB的等效設計,減輕了94%的重量,同時保持了高方向性和增益。采用CPD技術制造的喇叭天線,具有隔膜偏振器和蜿蜒波導過渡,展示了此方法在創建復雜內部通道方面的能力。其它示例包括折疊微型天線、分形幾何結構,以及使用彈性體和液態金屬合金的可拉伸設計。為了解決構建體積的限制,研究團隊設計了一種天線陣列模塊化平鋪策略,使得在不損失性能的情況下能夠組裝更大的孔徑系統。
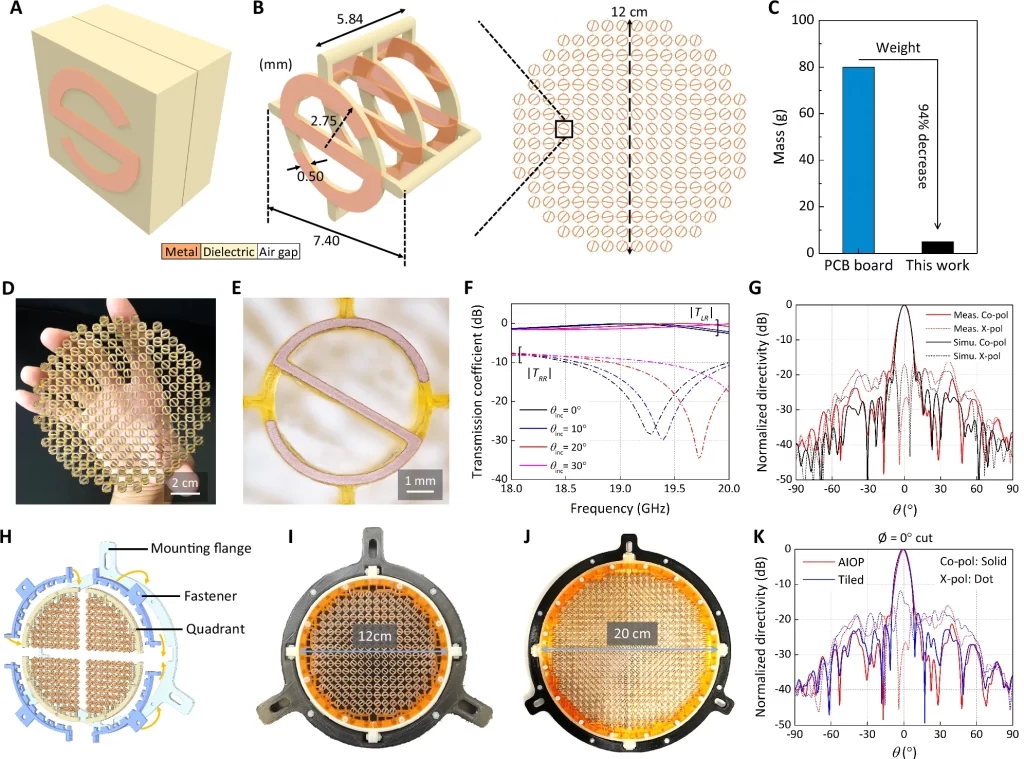
邁向可擴展、低成本的天線生產
與其它多材料增材制造方法不同,CPD工藝無需使用多個打印頭、復雜的基板對準流程或高溫燒結過程。相反,該方法基于標準SLA打印機,通過手動更換樹脂即可實現,具備成本低、操作簡便的優勢。研究中所探索的材料涵蓋聚合物、聚酰亞胺、陶瓷及彈性體,并通過定制樹脂配方以支持電荷調制與銅沉積。這項研究顯著降低了在空間受限或對重量高度敏感的平臺上制造定制化高性能天線的門檻。CPD工藝支持快速原型開發、設計迭代與按需制造,避免了材料浪費,以及減材制造或多步驟組裝帶來的復雜性。
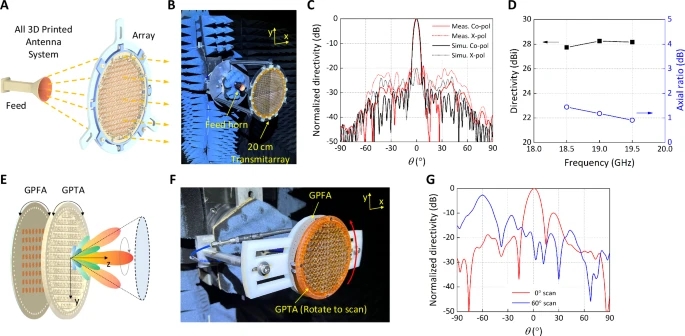
未來的研究方向將聚焦于樹脂處理流程的自動化、材料體系的進一步拓展,以及其它功能性涂層(如磁性或壓電薄膜)的集成,以滿足下一代電子系統的需求。這項工藝在立方體衛星、6G基站、便攜式和可穿戴設備等領域具備直接應用潛力,尤其適用于對重量、幾何尺寸與電性能要求極為嚴苛的場景。例如,具有很大的潛力應用于軍用雷達系統,包括復雜的相控陣雷達。早些時候,美國海軍研究實驗室利用3D打印技術制造優化的圓柱形天線陣列,與傳統方法相比,實現了更緊湊、更輕巧的設計。
(責任編輯:admin)